Filters
6 products
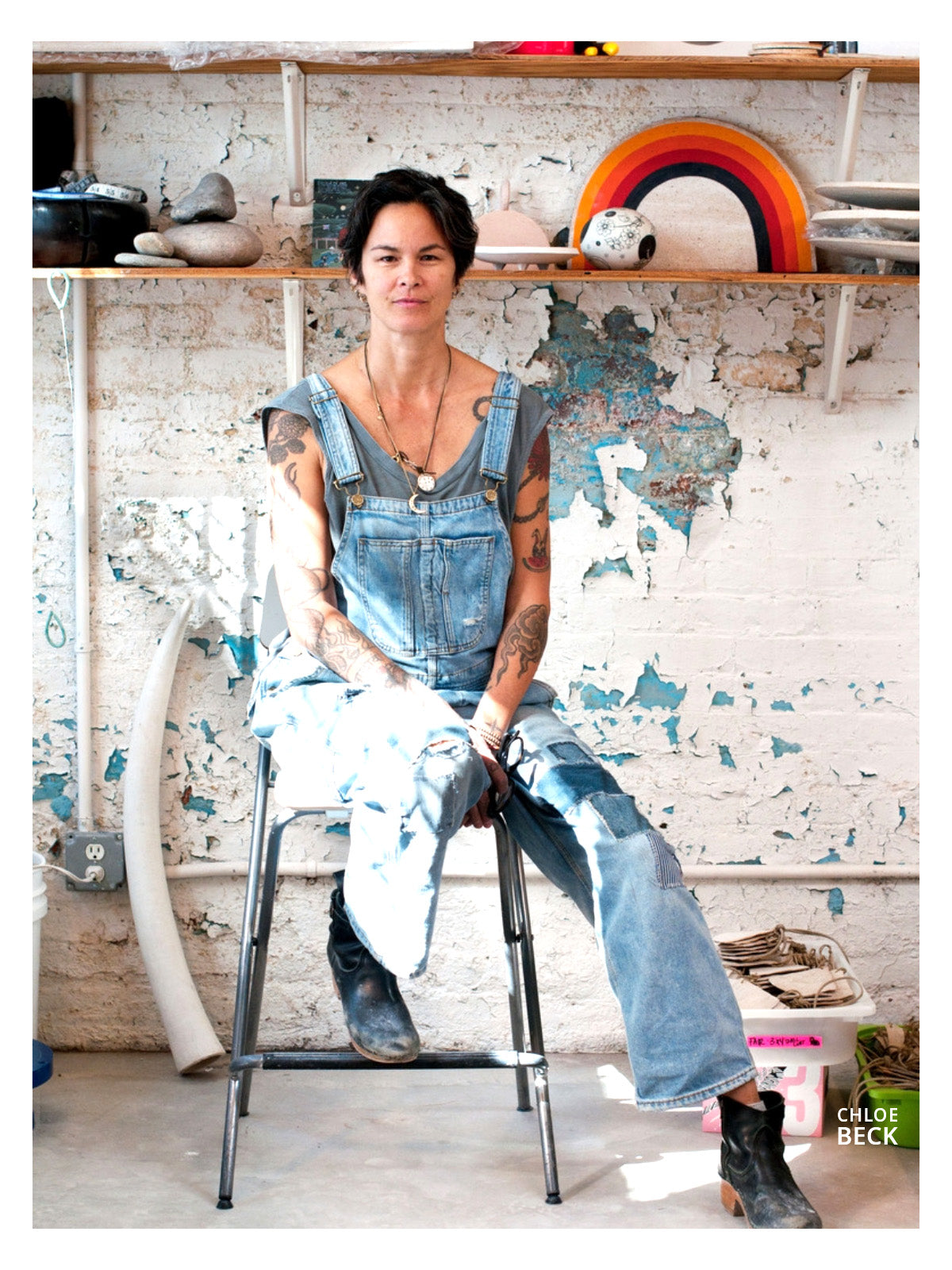
I make ceramic art & objects for the home and garden. The pieces become a canvas for my love of drawing, painting, text and color. Many of the objects and images are rooted in the visual symbols of Eastern iconography- their meaning and beauty of which I am continuously in awe.
Impermanence & interconnection are ideas that I return to often, drawing inspiration from the writings and teachings of Buddhism and its extensive visual language that points to the heart and the experience of living. I understand the meanings to be universal and independent of religious attachments.
All work is handmade in NY state by myself and a small team of talented and dedicated craftspeople. Stoneware forms are handbuilt or thrown on the wheel and all images are hand painted and then fired in a gas kiln to 2350 degrees. Other materials used include hand-dyed cotton, brass, wood & hemp rope.
A First Nations artist once said to me ‘Everything we need to know is in the sky’ and sometimes, when you look at the sky it can cut straight to the bone. It is this moment, in the midst of it all, that I try to convey. My hope is that the work serve both as objects of contemplation and as a source of encouragement, inspiring reverence. Although a little irreverence can go a long way, so don’t forget the rock n’ roll.
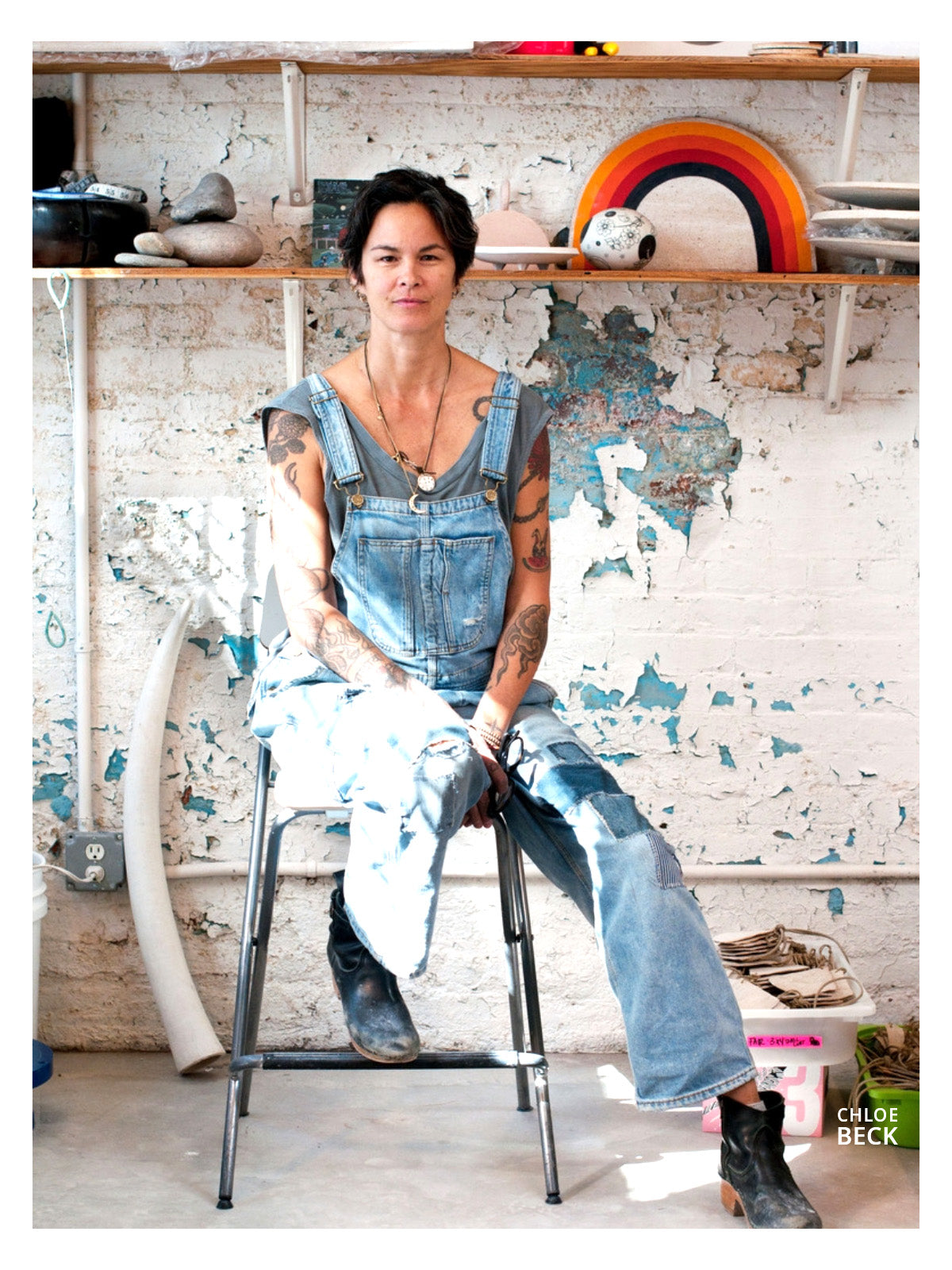
Materials & making, together with the reduction firing, give ceramic work 'depth and vibration'. We strive for consistency but also embrace the qualities inherent in the handmade ceramic process. Colors, sizes and shapes may vary between pieces, and no two are exactly alike, so please take that into consideration when purchasing.
Making: All the work is either built by hand, thrown on a wheel or a combination of the two. Images are painted by hand and fired onto the surface. Once fired, many pieces require extensive assembly.
Clay Body: Work is made from a custom East Coast stoneware with plenty of grog and iron that fires bare in a reduction kiln to a deep toasty brown. A few components, such as the Featherbones, are made from unglazed English Porcelain.
Grog is clay that has been fired, ground up, and re-wedged into the clay. Adding it creates ‘tooth’ allowing the clay to stand up better during building and aids to reduce warping & cracking while drying and shrinking. Visually it enhances the ‘stone-like’ texture and feel.
When the work is completely dry (greenware), the clay molecules are set and rigid without the water in between them that make it 'plastic' and malleable- this is clay in its most fragile state. It is then covered with multiple layers of white clay that are suspended in water.
Drying & Shrinkage: From wet to the final fired vitrified state, the clay shrinks about 10% as the water, both material and chemical, dissipate, and the clay molecules melt & fuse together.
To minimize warping & cracking during this movement, all of the parts, edges, & body of a piece, large & small, thick & thin, must dry evenly as they move while shrinking. To ensure even drying there is constant ‘babysitting’ (propping, flipping, covering etc). Large or flat pieces can take several weeks too dry to ensure the air gets to the all sides evenly or warping and cracking will occur. Many times these faults only present themselves after the work has been painted and gone through the final firing.
Bisque Firing: The first kiln firing is to approximatley 1725 degrees. The bisque firing is a 3 day cycle from start to cool. The clay, is now semi-vitrified, sintered and welded together. Strong enough to handle but porous enough for glaze to adhere to the surface.
Glaze Firing: Once the work is painted and/or glazed it is loaded into the gas kiln and fired to 2325 degrees. Gas firings are a 4 day cycle- Load, fire, cool, unload.
Assembly: Other components used are hemp rope, brass discs, cotton tassels & walnut or white oak wood. Rope ends are cut, whipped & assembled, wall hangings are knotted together with twine, knockers are assembled, cotton is dyed and torn, ceramic components combined.
I make ceramic art & objects for the home and garden. The pieces become a canvas for my love of drawing, painting, text and color. Many of the objects and images are rooted in the visual symbols of Eastern iconography- their meaning and beauty of which I am continuously in awe.
Impermanence & interconnection are ideas that I return to often, drawing inspiration from the writings and teachings of Buddhism and its extensive visual language that points to the heart and the experience of living. I understand the meanings to be universal and independent of religious attachments.
All work is handmade in NY state by myself and a small team of talented and dedicated craftspeople. Stoneware forms are handbuilt or thrown on the wheel and all images are hand painted and then fired in a gas kiln to 2350 degrees. Other materials used include hand-dyed cotton, brass, wood & hemp rope.
A First Nations artist once said to me ‘Everything we need to know is in the sky’ and sometimes, when you look at the sky it can cut straight to the bone. It is this moment, in the midst of it all, that I try to convey. My hope is that the work serve both as objects of contemplation and as a source of encouragement, inspiring reverence. Although a little irreverence can go a long way, so don’t forget the rock n’ roll.
Materials & making, together with the reduction firing, give ceramic work 'depth and vibration'. We strive for consistency but also embrace the qualities inherent in the handmade ceramic process. Colors, sizes and shapes may vary between pieces, and no two are exactly alike, so please take that into consideration when purchasing.
Making: All the work is either built by hand, thrown on a wheel or a combination of the two. Images are painted by hand and fired onto the surface. Once fired, many pieces require extensive assembly.
Clay Body: Work is made from a custom East Coast stoneware with plenty of grog and iron that fires bare in a reduction kiln to a deep toasty brown. A few components, such as the Featherbones, are made from unglazed English Porcelain.
Grog is clay that has been fired, ground up, and re-wedged into the clay. Adding it creates ‘tooth’ allowing the clay to stand up better during building and aids to reduce warping & cracking while drying and shrinking. Visually it enhances the ‘stone-like’ texture and feel.
When the work is completely dry (greenware), the clay molecules are set and rigid without the water in between them that make it 'plastic' and malleable- this is clay in its most fragile state. It is then covered with multiple layers of white clay that are suspended in water.
Drying & Shrinkage: From wet to the final fired vitrified state, the clay shrinks about 10% as the water, both material and chemical, dissipate, and the clay molecules melt & fuse together.
To minimize warping & cracking during this movement, all of the parts, edges, & body of a piece, large & small, thick & thin, must dry evenly as they move while shrinking. To ensure even drying there is constant ‘babysitting’ (propping, flipping, covering etc). Large or flat pieces can take several weeks too dry to ensure the air gets to the all sides evenly or warping and cracking will occur. Many times these faults only present themselves after the work has been painted and gone through the final firing.
Bisque Firing: The first kiln firing is to approximatley 1725 degrees. The bisque firing is a 3 day cycle from start to cool. The clay, is now semi-vitrified, sintered and welded together. Strong enough to handle but porous enough for glaze to adhere to the surface.
Glaze Firing: Once the work is painted and/or glazed it is loaded into the gas kiln and fired to 2325 degrees. Gas firings are a 4 day cycle- Load, fire, cool, unload.
Assembly: Other components used are hemp rope, brass discs, cotton tassels & walnut or white oak wood. Rope ends are cut, whipped & assembled, wall hangings are knotted together with twine, knockers are assembled, cotton is dyed and torn, ceramic components combined.
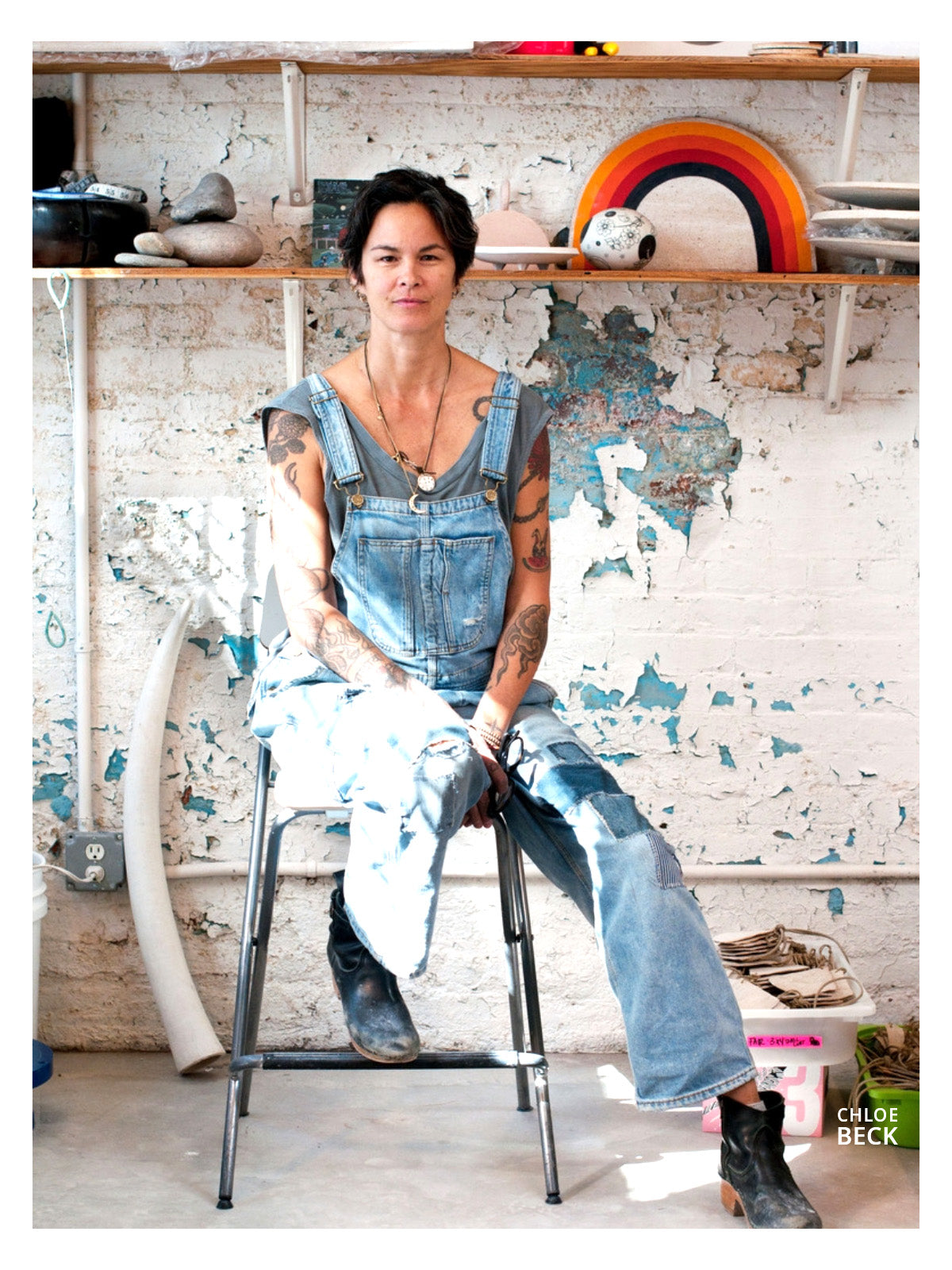
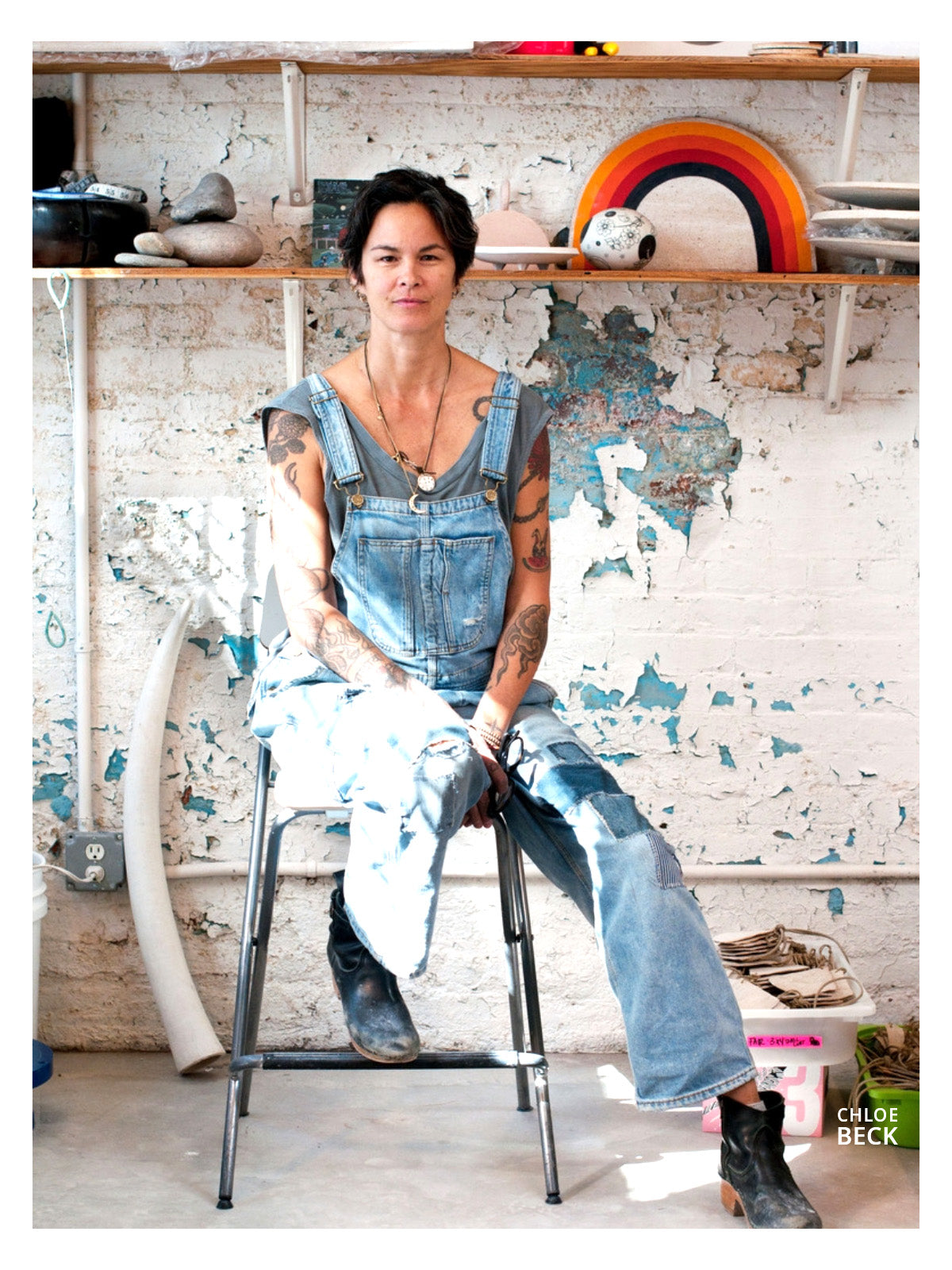